
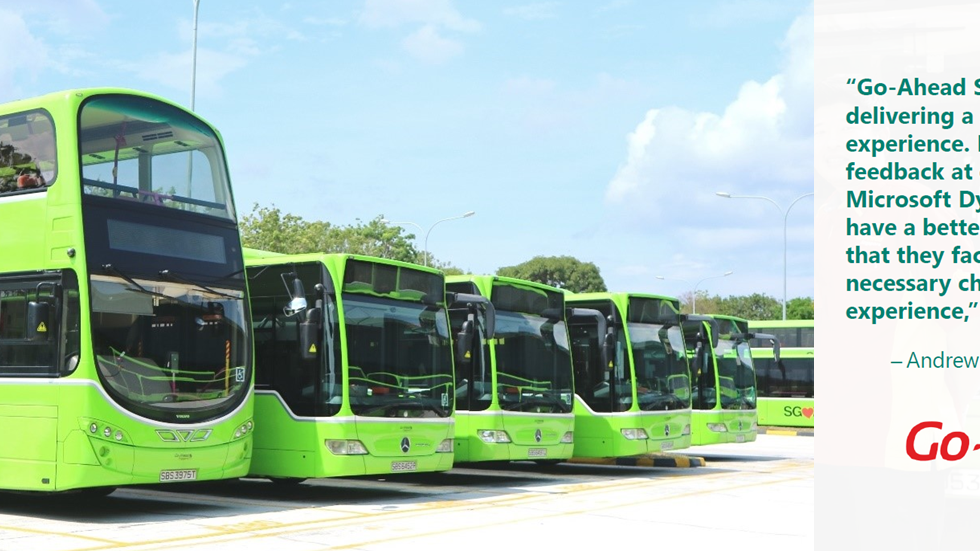
Go-Ahead Singapore: Customer-centric digital transformation to become the urban transport provider of the future
Go-Ahead Singapore is a leading local public transport provider and a subsidiary of the Go-Ahead Group, a UK transport operator. With a mission to create a world where every journey is taken cared of for everyone every time, Go-Ahead Singapore currently operates 28 services and are based at Loyang Bus Depot, serving the Punggol Bus Interchange and the Pasir Ris Bus Interchange.
Prior to the implementation of Microsoft Dynamics 365, Go-Ahead Singapore stored its data across various systems. However, as the company continued to expand to meet the growing demand for its services, there was a need for a new system that can work in synergy with the current systems, including the Common Fleet Management System (CFMS) and the Duty Allocation System (DAS), to improve its operational efficiency.
Since deploying Dynamics 365, Go-Ahead Singapore’s management team could easily gather information on bus captains’ performances and analyse it with ease, enabling them to identify areas of improvement that they can work on in future training sessions to plug performance gaps, and equip their bus captains with the necessary skills to excel in their roles in the future.
The system has also helped to improve the accuracy of the cash collection process for Go-Ahead Singapore. Today, the finance team can better keep track of the cash boxes on board their bus fleet, which are marked individually and linked specifically to each bus, to reduce the possibility of accounting mismatch and financial loss for the company as it continues to grow on the road ahead.
As for their customer service teams, the use of Dynamics 365 has helped to streamline the workflow and improve operational efficiency. “Microsoft Dynamics 365 is user-friendly and has a great overall experience. Three elements which I particularly appreciate are the ease of accessing commuter feedback, improved efficiency and a clean interface that does not overload a user with information,” said Tay Yu Ying, Customer Service Officer, Go-Ahead Singapore.
The consultants were very patient, have acute business sense and able to provide us with specific solutions that were inherent in our industry. This coupled with Microsoft’s assurance of support, thus gave us the confidence we needed to sign on the dotted line.
Mark Lui
Chief Information Officer, CWT Limited

M Manufacturing in Malaysia
M Manufacturing(not real name) in Malaysia is one of the world’s leading designers and manufacturers for generators and electric motors with worldwide brand recognition across four continents and two manufacturing facilities based in Europe and Malaysia.
The Challenge:
M Manufacturing needed a simple ERP system to start with for their new plant in Malaysia back in year 2009. They wanted a proven solution that is fast to implement, able to integrate well with the ERP data based in Europe headquarters as well as other systems, and comprises the features and functions of manufacturing, financial and supply chain management.
The Solution:
• Dynamics NAV 2013 R2 ( Upgraded from Nav 2009 Initial system ) with Financials Management, Manufacturing, Reporting, and Supply Chain Management
• Various integration to other system for data transfer
• Jet Reports
​
The Benefits:
M Manufacturing is exceptionally satisfied with the implementation of Dynamics NAV and here are some statistics .
• User growth : increase from 5 to 35
• 350% increase in production floor area
• Increase in production SKU from an initial 5 to the current 80+ SKU
The MNG group was very helpful and detailed, especially
Ms Gillian. We would love to work with the MNG group again.
Ian Ho
Director, Hall of Goods

NTX Manufacturing in Malaysia
NTX Manufacturing (not real name) is one of the leading manufacturers of high quality clean-room consumables and reusables. Their products are designed for controlled and critical environments where the focus is to eliminate contamination risk and improve customers' yields.
The Challenge:
Due to the rush of their initial system implementation, NTX Manufacturing faced the grave matter of massive data inconsistency which leads to time wastage in double checking data in ERP system for accuracy. Coupled with the increased demand in their manufacturing supply, they decided to go for a system upgrade to improve their system setup apart from sanitizing their data.
The Solution:
• Dynamics NAV 2017 ( Upgraded from NAV 2009 Initial system ) with Financials Management, Manufacturing, Supply Chain Management and Inventory
• Various integration to other system for data transfer
• Jet Reports
​
The Benefits:
NTX Manufacturing is able to continue using their existing system which they are familiar with for their daily operations with the added advantage of:
​
• More streamlined processes
• High accuracy of data output
Having GSS as partner helped to win the hearts of the people, as they understand our requirements very well and always provide prompt response to our issues. We are so pleased with the partnership therefore we have extended GSS’ role become our global Navision implementer for Leong Jin.
Ivan Ho
General Manager, Leong Jin Corporation Pte Ltd

PT Distribution in Singapore
PT Distribution (not real name) is one of the key players in the wholesale trade of international fragrances. Their principal activity centers around importing and exporting fragrances for their subsidiaries.
The Challenge:
Without a proper centralized ERP system, PT Distribution was ill equipped to handle the rapidly changing demands for the goods they distribute in the FMCG industry. Coupled with the ever-growing demand in their supply volume, tracking incoming and outgoing inventories for multiple subsidiaries then became a challenge as it was a tedious and time-consuming process and also more prone to errors. The inconsistency in data recording resulted in discrepancies in inventory records. Therefore, PT Distribution decided to adopt Microsoft Dynamics NAV which offers a rich suite of features to help them automate and connect their business processes smoothly.
The Solution:
• Dynamics NAV 2016 with Financials Management, Supply Chain Management and Inventory
• Easy Security
The Benefits:
Microsoft Dynamics NAV has enabled PT distribution to develop a special customized process that is unique to them and allows them to computerize all master data apart from streamlining their business processes.
With NAV 2016, PT Distribution was also able to:
​
​• Consolidate and file their data with proper versioning, proper track records and audit trail
• Customize the system into allowing them to allocate all their subsidiaries’ stocks in 1 warehouse, with real-time updates
ABPGroup partnered with MNG Solutions in 2019 to integrate Microsoft Dynamics 365 Business Central into our diverse business operations. This collaboration brought about a remarkable transformation.
By leveraging Business Central, ABPGroup streamlined our financial processes, reducing manual errors and improving overall efficiency. MNG Solutions customized the platform to align with our unique needs, ensuring a seamless integration across various business units.
The centralized data management capabilities of Business Central empowered ABPGroup with real-time insights into our operations, enabling faster and more informed decision-making. With MNG Solutions' expertise, the transition was smooth, minimizing disruption to our day-to-day activities.
The integrated solution not only enhanced our internal processes but also improved collaboration among different departments. As a result, ABPGroup experienced increased productivity and a significant reduction in operational costs.
In summary, the collaboration between ABPGroup and MNG Solutions, powered by Microsoft Dynamics 365 Business Central, not only modernized our business processes but also positioned us for sustained growth in a dynamic market.
Jerrylyn Dionisio
Senior Operations Manager, ABPGroup Pte Ltd